“Planed Tight Contact”—Does It Mean No Welding Is Required?
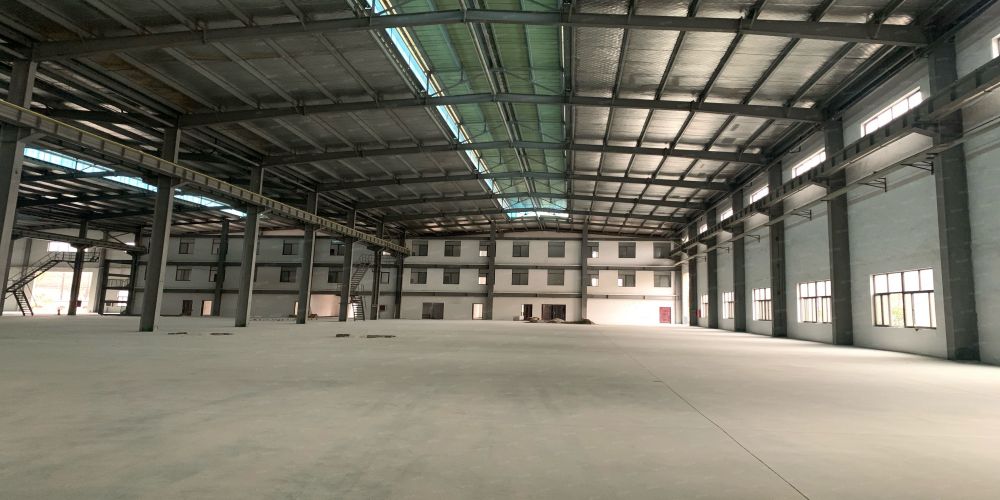
Polished tight contact is a load transfer method commonly used in locations subjected to dynamic loads. It is a technique to prevent fatigue cracks in welds. Some designs specify that polished tight contact does not require welding, while others do. The final requirement depends on the specific drawings. The contact surface must have a smoothness of no less than 12.5 and should be checked with a feeler gauge for the contact area.
The purpose of planed tight contact is to increase the contact area, typically used in joints with some horizontal displacement or simple support connections. These joints should also have additional connection methods (e.g., tight contact of the flange while the web might be bolted). Generally, areas requiring planed tight contact do not require welding. If welding is necessary, planed tight contact is not conducive to deep penetration of molten metal, leading to poor weld quality. Even if welding is needed, the planed tight contact area will not be required for full penetration welding.
Tight contact and welding are inherently contradictory. Therefore, stating that welding is required in tight contact areas is not entirely accurate. However, there is one exception: if the joint lacks sufficient restraint in other degrees of freedom and no other constraints are provided, welding may be applied at the tight contact area to restrict movement in other directions. This type of weld is considered an installation weld, not a full-strength weld, and is not meant to be the primary load-bearing weld.